Every business involved in the product market requires inventory in raw materials, labour, packaging. It is crucial to maintain an inventory to deliver products on time and with efficiency. However, having an inventory can incur additional costs due to maintenance requirements, wastage, space etc. This article will discuss inventory management and how you can reduce costs through a just-in-time inventory management system.
What is Just-in-Time Inventory?
Just-in-Time Inventory involves:
- Storing and managing inventory, so they arrive only when required for the business.
- Ensuring minimal storage.
- Minimal Wastage.
- Increased efficiency in the production process.
The system also allows for efficient and cost-effective production processes.
This system was first adopted by Toyota and a few other Japanese companies. Today this method is used by many small and large scale businesses to process and manage their inventory. The key in Just-in-Time inventory management is to understand the demand and supply of the business efficiently to manage the inventory requirements in the best possible way.
Common misconceptions are that this method slows down the delivery time and production process, making it unviable for businesses. But these problems only occur due to the flaws in management and implementation of the process and not by the process itself.

How to Create a Just in Time Inventory Management System?
Here are a few steps that you can follow in order to create a Just-In-Time inventory system:
- Continuous assessment: In order to create an efficient inventory storage system, it is essential to fully understand the nature of demand and supply in your business and the pattern in which it fluctuates. Understanding these aspects of the business will help you in assessing when you require what. For example, if you run a business of readymade clothing, festivals are a time of high demand, but monsoons are not. So you can tweak the stock with you, according to it.
- Assess and reevaluate supply chain: Supply chain is where the raw materials for businesses come from. Often these supply chains require bulk purchases and therefore create a heavy inventory with the business. In order to resolve this, you can reevaluate your vendor options and find vendors that can accommodate your just-in-time system. This may lead to small additional costs initially but will add up and save money in the long run.
- Labour management: Labour and human resources are a part of the inventory of the business. Often, labour costs are ignored by businesses. But it is essential to evaluate the business's labour needs and accommodate resources more efficiently. One of the best ways to incorporate this is through hiring freelancers and gig workers. This allows you to hire and pay employees only according to work done and provides freedom of time to the employees. This ensures efficient use of labour and can help save costs.
- Invest in technological tools: One of the biggest challenges of Just-In-Time inventory is to ensure timely management of ordering and delivering products. But specialised tools and organisation methods can make this process simpler. One of the best tools to manage labour is OkStaff. The tools allow you to calculate and manage payroll to be more efficient without any hassle. Other automation tools can also be used to auto-create lists and order requirements.
- Set Limits: Most businesses regularly stock up on their inventory every month. However, switching this to a requirement based method can help in creating a better system. For example, if you run a jewellery business, you do not order new until you reach a lower limit on your stock. This method will set a limit on your ordering rather than running it on auto-pilot.
These are just some essential steps that you need to undertake to implement this inventory model. The JIT system is very flexible. Hence, you can adopt other methods and measures to create a perfect system for you and your business requirements. An analysis of other businesses within your industry can also help in getting more information about the process.
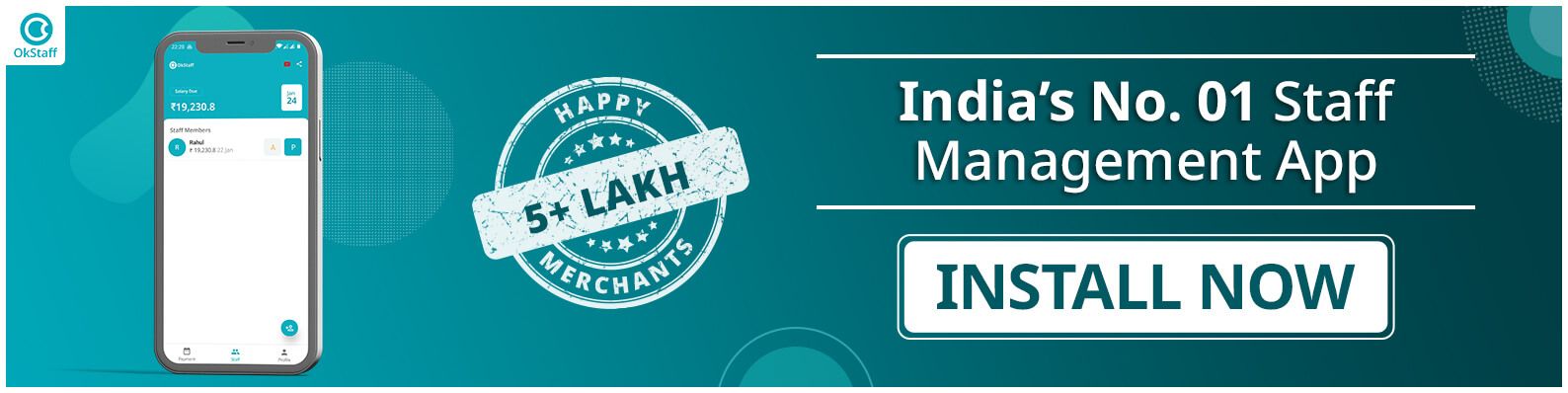
Advantages of Just in Time Inventory
Some of the most significant advantages of the Just-In-Time Inventory are:
- Cost efficiency: Limited inventory ensures you save money on raw materials, storage, etc. This helps in saving costs and ensuring you have more cash flow in your business.
- Reduce waste: Waste reduction is one of the most significant benefits of this system. Since a limited and required quantity of materials is used, it ensures that you do not waste any resources.
- Easier management: Limited inventory and stock mean limited control and management, which will save you time. This will allow you to focus better on other aspects of the business.
- Better quality: Increased cash flow due to limited inventory allows you to invest in better quality products.
- Efficient production: The JIT system allows you to focus on the required number of products, which means it creates an opportunity for a better production process. This ensures that products are made with more time and focus, minimising mistakes and increasing efficiency.
- Flexibility: There is no one size fits all approach to the just-in-time inventory model. Each business runs differently, and its requirements are different. But this method is highly customisable and allows businesses to be flexible in their approach.
Disadvantages of Holding an Inventory
Some of the most significant disadvantages or troubles that come with holding an inventory are:
- Storage costs: Any inventory incurs storage costs. These costs are added in perishable goods and goods that require special conditions such as food, cosmetics etc.
- Excessive storage: Excessive inventory storage is a common problem in most businesses. Excessive inventory can lead to wastage and cause losses to the company.
- Reduced investment resources: Inventory costs significantly reduce the cash flow available to businesses. Reduced cash flow can put the company in debt and increase costs.
- Insurance costs: Excess inventory increases insurance costs to protect it from any accidental damages.
While these disadvantages exist, no business can eliminate having an inventory. But using intelligent inventory management tools can help in reducing these risks while not affecting the business.

Things to Keep in Mind Before Adopting the Just-in-Time Inventory Model
- Give time: The method is complex and can take a while to perfect. Thus, be prepared to invest some time before you perfect it. Have some backup options to fall back on in case your calculations make an error.
- Go slow: In connection with the previous point, it is vital to adopt this process slowly. Bring in small changes as opposed to radical ones. Changes in inventory models can cause trouble to vendors, employees and others involved in the production process. Hence, it is better to be mindful of these consequences and be prepared for these changes.
- Prepare for failures: As much as you would like to, there are going to be errors that will occur in the process. Instead of denying them, it is best to be prepared for such occurrences.
- As efficient and flexible as the Just-in-time inventory model is, various factors determine the success of this method. Hence, at a particular time in your business, this method may not be suitable for you. But businesses must constantly evaluate and try this method at every stage.
With these steps and tools, you can implement a Just-in-Time Inventory management system and save on costs, reduce wastage and smartly plan your business requirements.
Also Read:
1) 7 Mistakes You Need to Avoid For Reducing Logistics Costs
2) 10 Tips on How to Manage your Left-over Inventory
3) Tips and Tricks To Sell Your Product in Marketplaces
4) Top 10 Sources to Get Your Startup Funded
Stay updated with new business ideas & business tips with OkCredit blogs in English, Hindi, Malayalam, Marathi & more!
Download OkCredit now & get rid of your bookkeeping hassles.
OkCredit is 100% Made in India.
FAQs
Q. Does my business need the Just-in-Time inventory model?
Ans. This model is best suited for manufacturing businesses. Within that, every business can benefit from this system.
Q. What tools can I use to manage my inventory?
Ans. Tools like OkCredit and OkStaff help in analysing and managing finances, staff payroll and accounting. They automate the process, so it does not require heavy time investment from your end.
Q. How do I measure my inventory requirements?
Ans. Depending on the kind of business, you can order and prepare your inventory based on the demand. But to ensure quicker delivery of products, you can analyse your average request and prepare accordingly.
Q. Are there any disadvantages of the Just-in-time inventory system?
Ans. Not a disadvantage, but finding the perfect balance can be challenging at times. This challenge often discourages many business owners from adopting this method.
Q. Where can one use the resources saved from this method?
Ans. Businesses can use the saved costs and resources for the growth of their business. For example, for marketing, branding, improved quality etc.